Out with the old, in with the new: How a tie gang replaces ties
On an early winter morning at BNSF’s South Yard in Amarillo, Texas, despite the cold and accumulated snow, an Engineering tie gang starts their day. The task at hand: replace one wooden tie after another on a stretch of track within the yard. It's a well-orchestrated process.
For many railroad enthusiasts, ties are an afterthought. The locomotives, the rail cars and even the rail itself generally capture the spotlight. But it goes without saying that a railroad is nothing without ties (wooden, concrete, steel or composite) and the teams who maintain them. Without proper tie conditions, we couldn't operate trains.
If you haven't had the opportunity to see a BNSF tie gang in action, these photos help tell the story of the impressive work they do.
The Prep
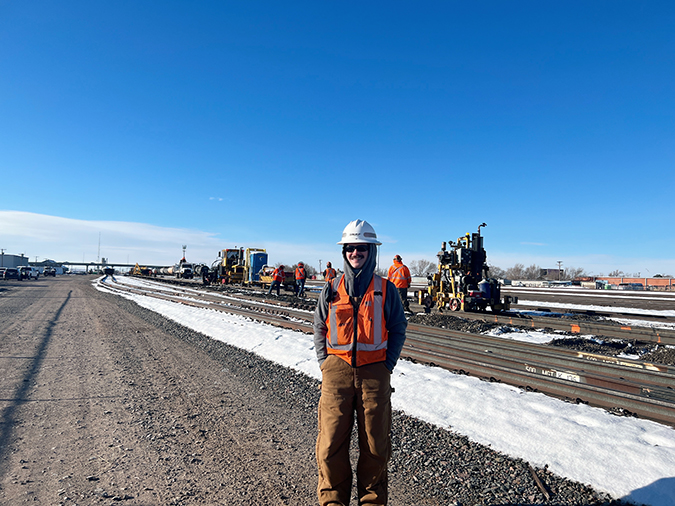
Generally, not all ties along a specific line are replaced all at once. The initial step involves inspecting the ties. The process starts by evaluating ties for signs of wear and fatigue. In this case, it's a manual effort where inspectors mark the location of ties to be replaced with an orange mark painted on the rail. On this morning, the ties to be replaced are already identified and the gang in position. Helping to lead the team is Brady Sewell, assistant roadmaster for our Kansas Division.
The average lifespan of a tie varies by geographic location, track type and quality of the tie. But, in general, a new cross tie on a yard track in the Texas Panhandle could expect to be in place for decades.
The Pull
Physically switching out ties begins with a unique contraption aptly called the “spike puller." The machine has a set of claws that targets the spikes — the large “nails” that secure the rails to the ties — grabs them and pulls them out, leaving only the tie plate and the old tie.
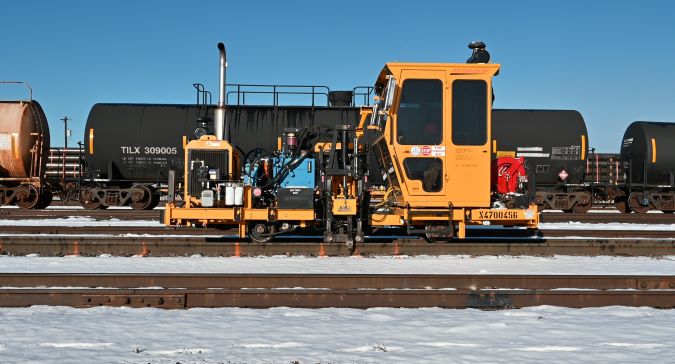
The Slide (Out then In)
The next machine on the line, called a Tripp machine, lifts the rail slightly, latches onto the end of each 8-1/2-foot tie and gently slides it out from beneath the rail.
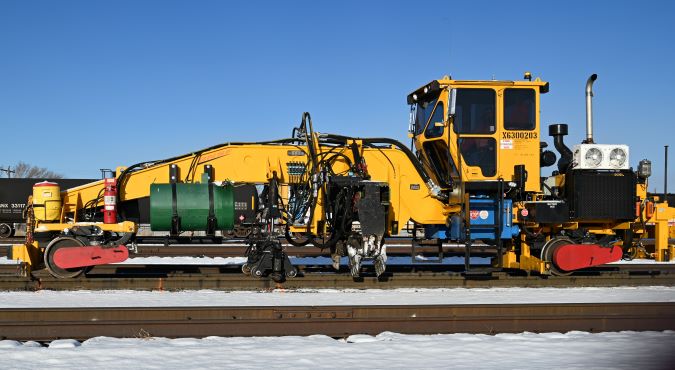
Usually, two tie cranes are positioned right behind the Tripp machine. One of the cranes stacks the old ties. The other crane follows and positions the new ties neatly into position perpendicular to the rail where the previous ties were.
Next, another Tripp machine latches onto the new tie and carefully slides it into place under the rail.
The Spike
Ground crew members follow the second Tripp machine. They're on foot and their role is to position the plates on the new tie. Another machine clamps onto the rails, lifts them just enough for the crew members to safely slide the plates underneath the rail – one on each side.
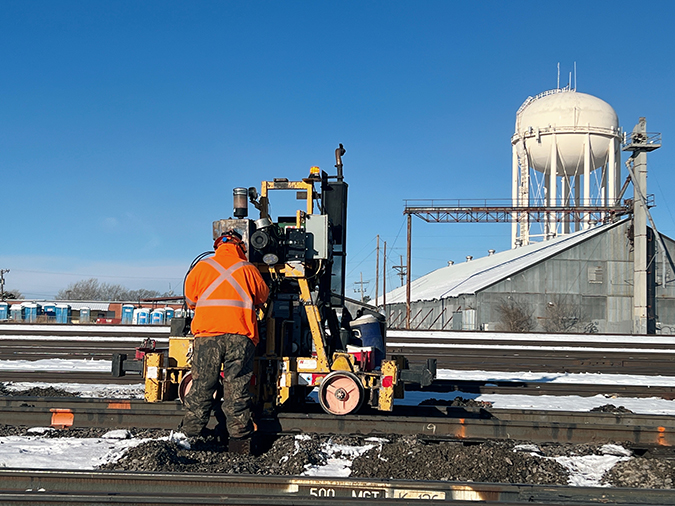
The stage is now set for the spikes to be driven into the tie, securing the rail in place. In the old days, of course, this was a completely manual effort using spike mauls. But, today, a machine safely and efficiently pounds the spikes into the tie, greatly reducing risk—not to mention sore shoulders and backs.
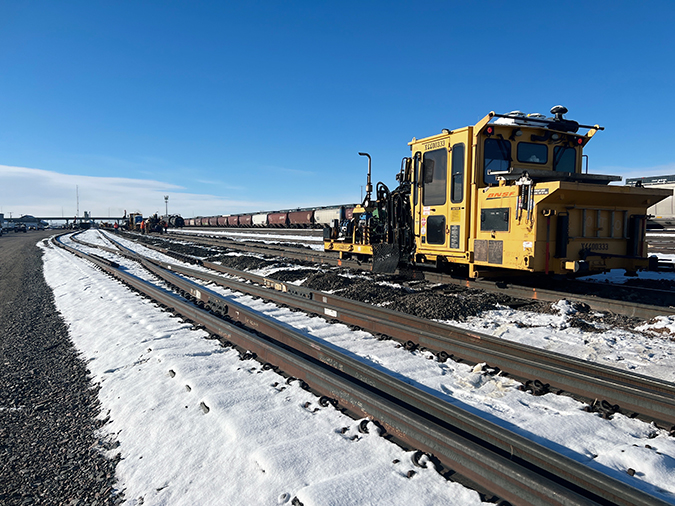
The Restoration
Finally, once the spike-driving machine is a few hundred feet ahead, a surfacing crew will follow with a tamper (not pictured) that is used to lift, level and line the track. Following the tamper, the surfacing crew uses a ballast regulator (not pictured) that smooths out the ballast and restores it to its original profile before the work began.
With so many pieces of equipment, there's always a chance of mechanical failure. That’s why a mechanic is assigned to most tie-replacement crews to repair equipment when needed, minimizing delays.
The Disposal
What happens to the old ties? In general, they’re picked up and sold to a third-party entity that markets them for use elsewhere and/or for other purposes. Our Engineering team typically uses grapple trucks to remove the ties from trackside immediately after replacement, then stages them for loading into gondolas or onto trucks.
The Pace
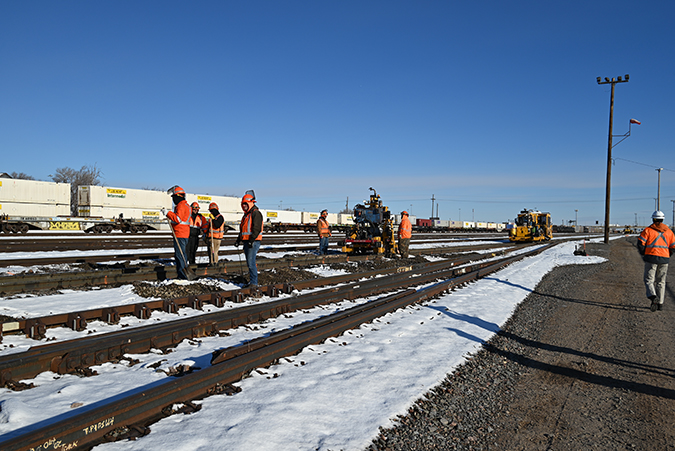
A lot of factors can dictate the productivity of a tie-replacement gang. But for this Kansas Division crew, their production goal for each 7-hour day is 200-plus ties.
Special thanks to all the tie-replacement crews across BNSF. As professionals, they make hard work look easy—and do it safely.